その他・コラム
FEATURE DETAIL
その他・コラムコラム
機械の安全化とリスクアセスメント手順について
機械の安全化とは
国際規格では、安全を「許容可能なリスクに抑えられている状態」(ガイド51)と規定しています。
つまり絶対安全というものはなく、いくらかリスクは残ることを前提としており、許容可能なリスクは「社会の現在の価値観に基づいて、特定の状況で受け入れられるリスクのレベル」とされています。
機械の安全化とはリスクを許容可能なレベルまで抑えることであり、個々の機械のリスクは製造者が実際の機械の使用状況に合わせたリスクの評価・対策を行うことが求められています(リスクアセスメント)。
つまり絶対安全というものはなく、いくらかリスクは残ることを前提としており、許容可能なリスクは「社会の現在の価値観に基づいて、特定の状況で受け入れられるリスクのレベル」とされています。
機械の安全化とはリスクを許容可能なレベルまで抑えることであり、個々の機械のリスクは製造者が実際の機械の使用状況に合わせたリスクの評価・対策を行うことが求められています(リスクアセスメント)。
リスクアセスメントの進め方
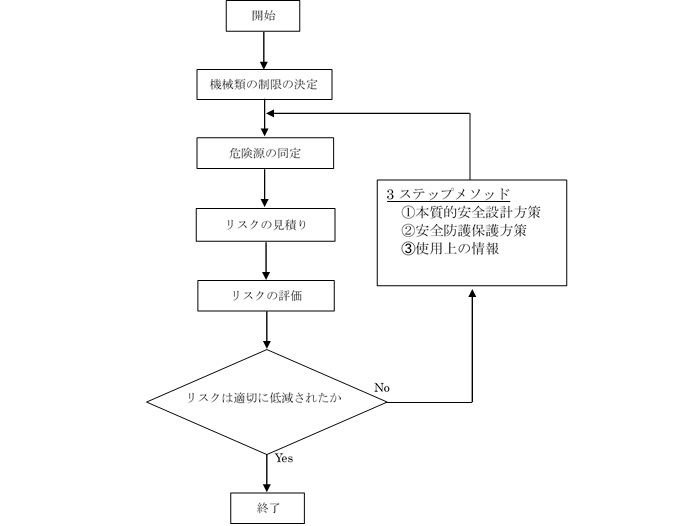
リスクアセスメントの進め方はISO12100で規定されており、上図のフローチャートはISO12100で定められたリスクアセスメントの手順です。
機械類の制限の決定
機械の製造者は次に掲げる機械の制限に関する仕様を指定することから始めなければなりません。
・機械の意図する使用、合理的に予見可能な機械の誤使用
・機械の動作、設置、保守点検等に必要とする範囲等の空間上の制限
・機械、その構成品及び部品の寿命等の時間上の制限
・機械の意図する使用、合理的に予見可能な機械の誤使用
・機械の動作、設置、保守点検等に必要とする範囲等の空間上の制限
・機械、その構成品及び部品の寿命等の時間上の制限
危険源の同定
機械の製造者は機械によって引き起こされる可能性のある種々の危険源を同定しなければなりません。
危険源の同定は機械の通常使用だけを想定するのではなく、運搬、設置、試運転や予見可能な誤使用など機械のライフサイクル全てが検討の対象となります。
危険源の同定は機械の通常使用だけを想定するのではなく、運搬、設置、試運転や予見可能な誤使用など機械のライフサイクル全てが検討の対象となります。
リスクの見積り
同定した危険源に対してリスクの大きさを見積もります。リスクの大きさは「危害のひどさ」と「危害の発生確率」で評価されます。「危害の発生確率」は「危険源への暴露頻度」「危険事象の発生確率」および「危害回避の可能性」を組み合わせて見積もってよいとされています。リスク見積もりの際、いくつかのツールが利用可能でありリスクマトリクスやリスクツリーなどがあります。
リスクの評価
リスクの評価とはリスクの低減が必要であるかどうか、リスク低減目標を達成できたかどうかを評価します。リスク低減が必要であると評価された場合は、リスク低減方策を適用させる必要があり、リスク低減は以下に述べる3ステップメソッドの順番に従って実行されなければなりません。
リスク低減方策(3ステップメソッド)
①本質的安全設計方策
設計による危険源の排除が行えないか検討します。危険源そのものを無くしてしまうことができれば、最も効果的な方法となりますので最初に優先して取り組むべき対策内容になります。
②安全防護保護方策
製品機能に影響を及ぼしてしまう等の理由により本質的安全設計が行えない場合は、安全防護保護方策を行います。危害は危険源と人が接触した際に発生しますので時間的、空間的な隔離を目的とします。
・停止による安全防護:人の接近を検出し機械を停止させ、時間的に人と危険源を隔離します。
・ガードによる安全防護:危険源に近づけないように防護柵を設ける、飛散を避けるために密閉する等、
人と危険源を空間的に隔離します。
③使用上の情報
本質的安全設計、安全防護柵ではリスクが除去、または低減できない場合は使用上の情報を用いて使用者にリスクを明確に伝えなければなりません。技術的に対応可能なものを情報提供で代替してはいけません。
1.取り扱い説明書
機械の取り扱い、保管に関する情報、残留リスクの情報、残留リスクを回避する為の情報、必要な訓練など
2.信号・マーキング
表示灯、標識、警告文など
3ステップメソッドを行った後、再度危険源の同定、リスクの見積もりを行います。対策を行ったことにより新たなリスクが発生していないか注意が必要です。最終的に設計した機械のリスクが許容可能なレベルになるまでリスクアセスメントのフローを繰り返します。
設計による危険源の排除が行えないか検討します。危険源そのものを無くしてしまうことができれば、最も効果的な方法となりますので最初に優先して取り組むべき対策内容になります。
②安全防護保護方策
製品機能に影響を及ぼしてしまう等の理由により本質的安全設計が行えない場合は、安全防護保護方策を行います。危害は危険源と人が接触した際に発生しますので時間的、空間的な隔離を目的とします。
・停止による安全防護:人の接近を検出し機械を停止させ、時間的に人と危険源を隔離します。
・ガードによる安全防護:危険源に近づけないように防護柵を設ける、飛散を避けるために密閉する等、
人と危険源を空間的に隔離します。
③使用上の情報
本質的安全設計、安全防護柵ではリスクが除去、または低減できない場合は使用上の情報を用いて使用者にリスクを明確に伝えなければなりません。技術的に対応可能なものを情報提供で代替してはいけません。
1.取り扱い説明書
機械の取り扱い、保管に関する情報、残留リスクの情報、残留リスクを回避する為の情報、必要な訓練など
2.信号・マーキング
表示灯、標識、警告文など
3ステップメソッドを行った後、再度危険源の同定、リスクの見積もりを行います。対策を行ったことにより新たなリスクが発生していないか注意が必要です。最終的に設計した機械のリスクが許容可能なレベルになるまでリスクアセスメントのフローを繰り返します。
おすすめする安全機器 セーフティレーザスキャナ
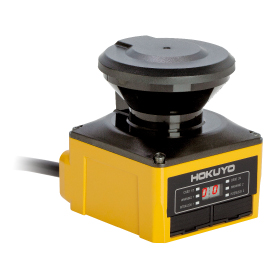
セーフティレーザースキャナUAM-05LP-T301
防護領域5m、270°の範囲を自由なエリア設定で検出するセーフティレーザスキャナ。小型、高機能と使いやすさの両方を兼ね備え、AGV(無人搬送台車)、ロボット、機械などへの安全対策で工場や物流の効率化、稼働率の向上が可能。防護柵、ライトカーテンやマットスイッチの置換えに。安全規格認証機器PLd。
もっと詳しい内容を知りたいなら
防護領域5m、270°の範囲を自由なエリア設定で検出するセーフティレーザスキャナ。小型、高機能と使いやすさの両方を兼ね備え、AGV(無人搬送台車)、ロボット、機械などへの安全対策で工場や物流の効率化、稼働率の向上が可能。防護柵、ライトカーテンやマットスイッチの置換えに。安全規格認証機器PLd。
もっと詳しい内容を知りたいなら
関連コラムを読む
製品カテゴリ
- 測域センサ
- 光電・レーザーセンサ
- 鉄鋼・クレーンセンサ
- 応用システム
- 光データ伝送装置
お役立ち情報